For a passive solar home I prefer a slab on grade
construction. The concrete in the slab acts as a significant heat
sink to stabilize the temperatures in the house. The slab adds about
45,000 lbs of mass that takes a long time to heat up and a long time to
cool off. So the house heats up slowly when the winter sun
shines in and then the warmed slab helps keep the house comfortable
through the evening. Without mass a house can get too warm on a
sunny winter day and then quickly cool off after sunset. |
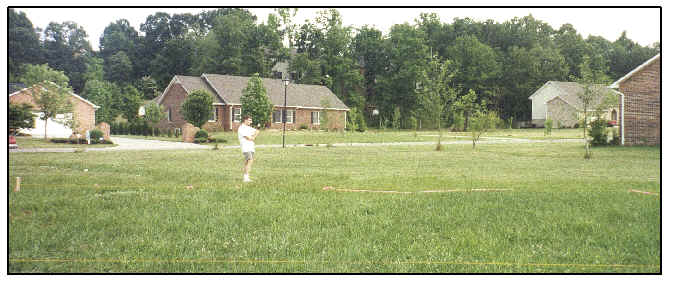 |
The house is located in a typical suburban
neighborhood. For the proper orientation the main house sits at a 45
degree angle on the lot but since the garage is square to the street it
fits in quite nicely with the neighborhood. |
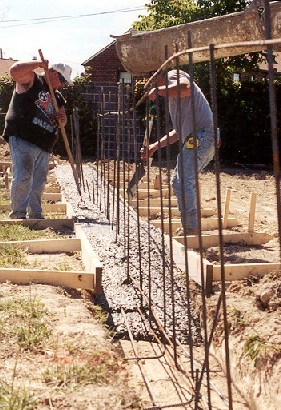 |
We needed a more substantial footer than most homes
because ICF's, when filled with concrete, are far heavier than a standard
wall. I also like a solid footer so my preference is to build then
larger and add more steel than code requires. This also gets you off
to a good start with city inspectors. Mine were 14" thick and
24" wide.
I used 4 # 4 rebar around the perimeter and then had vertical rebar every
8" to tie into the ICF wall.
While part of the footer may appear to be above grade, after grading the footer is at least 2' below
the ground level. |
 |
The footer around the garage does not have the vertical
rebar as it is a standard frame wall. But you can still see short
rebar sections to tie into the slab |
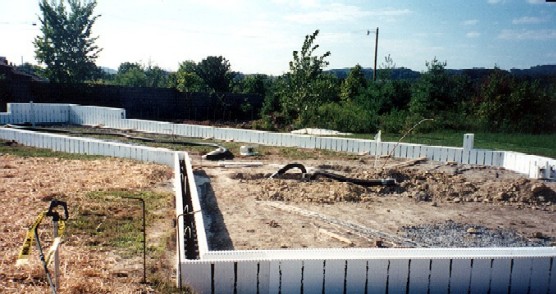 |
An ICF/SIP house is VERY tight by design. So I wanted
to control air infiltration.
The black pipes you see are part of an air intake experiment. As
we dug trenches for water lines I buried the 100' long pipe about 3' below
the ground. They come up under the air intake for the heat pump.
This allows us to control air infiltration by allowing
air heated by the earth in the winter and cooled in the summer to enter
the house. This did not work well as 2 of the 3 pipes filled with
water and had to be capped. |
 |
We using over 125 ton of gravel under the
slab. About 50 tons more than initially estimated. I realized that shoveling would take far too long.
On the average we have a 13 inch bed of gravel. One of several
cost overruns we experienced.
Besides a bobcat is much more fun than shoveling all day
long. One thing I found was that for a novice the bobcat is not very
stable and it can easily get away from you.
After the gravel was
placed we used a tamper to compact the gravel and we put sprinklers on all
night for further consolidation.
|
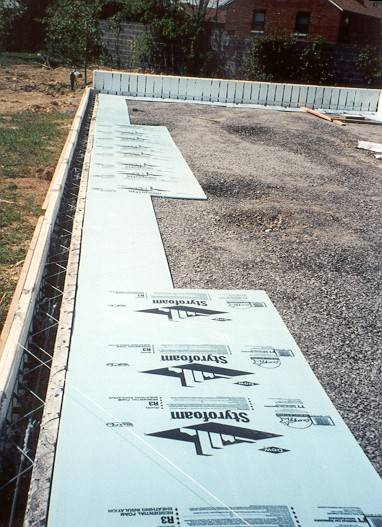 |
We used the outside of the ICF to insulate the edge of the
slab. This gives nearly 3" of excellent insulation at the edge of the
slab.
We placed Styrofoam insulation around the perimeter to help keep the
floor warm in the winter. It has worked as the sun keeps the floor
comfortably warm in the winter. |
 |
We spent a significant amount of time checking and
rechecking our plans and layout as we went. Since we designed the
house ourselves we wanted to catch any mistake before it became an
expensive alteration. |
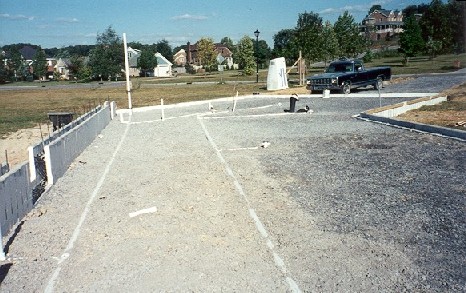 |
Plumbing lines before the slab was poured. We ran dual
lines in case there was a future problem.
The black pipes sticking up
are for the air intake. I would only recommend on a slopped lot
where the pipes can easily drain. Two of ours filled with ground
water. However, the one working one does do a good job of moderating
the incoming air.
I also added a thermal break in the slab
between the garage and the house.
|
 |
We added an emergency cut over if one of the sewer lines
becomes broken under the slab. |
 |
Before the pour we covered the gravel with
plastic. This helps the concrete cure slower which results in fewer
cracks and a stronger floor. |
 |
For the parts of the slab that would have a frame wall we
inserted anchor bolts every 2 1/2 feet to ensure the walls were attached
securely. Again this is double the amount required by code.
After traveling to Europe we decided we wanted to build a home that would
last.
|